![]() ![]() ![]()
Какой рейтинг вас больше интересует?
|
Главная /
Каталог блоговCтраница блогера 3D-принтеры сегодня!/Записи в блоге |
![]() |
|
Любителям сварочного дела...
2017-07-06 21:59:42 (читать в оригинале)Так случилось, что у моего сварочного аппарата сломался электрододержатель (держак). Прямо по металлу по цветному разлом пошел...
Не проблема в наше время. Приобретается изделие ЭД-300 на 300А в ближайшем сетевом магазине ( не будем делать рекламу), но тут разваливается рукоятка. Прямо так, на куски. И, как обычно, в самый не подходящий момент.
Вот не везуха, думаю, и спешу в другой сетевой магазин купить держак. Коробка один в один. Выбора нет. Работа стоИт...
Не смотря на одинаковое название и похожую упаковку, конструкция держаков разная. Во втором случае (на фото в верней половине) явно на 300А не тянет. Тонкая омедненная сталь, Но рукоятки то на одном пресс-автомате похоже делали!

Ну не удобная она. И конструктивные недостатки: изнутри к цилиндрической поверхности прижимаются плоские детали, а в момент смены электрода идут напряжения в пластике и он либо вырываестя, либо лопается.
К чему все это?
Решил улучшить конструкцию рукоятки.
В начале смутило, что на коробке написано: "Термостойкая изолированная ручка".

Ха: 280 градусрв и жало паяльника прожгло ее насквозь! Сомнений больше нет. За дело!
Смоделировал ручку сразу для двух типов электрододержателей. Назвал их Тип А и Тип В. STL-модели здесь
Сделал все приливы внутри.
Выполнил изоляционные буртики у зажимного винта (тип В)
Увеличил конусность внешней поверхности - удобнее в руке лежит
И распечатал из оранжевого пластика PROTOTYPER S-SOFT

Вот конечный результат:

Подробнее...
Спасибо, Анет! Пора двигаться дальше.
2017-07-06 21:04:26 (читать в оригинале)На момент покупки моего Анет А8 я не знал о 3D-печати ничего. Впринципе, это и было причиной выбора принтера подешевле, так сказать на пробу.
За время, потраченное на бесконечные доделки и переделки принтера, я понял несколько вещей:
1. 3D-печать это то хобби, которым я хочу заниматься всерьез ближайшие несколько лет.
2. Руки у меня выросли из нужного места

3. Возможности Anet A8 очень сильно ограниченны даже после множественных доработок.
Принтер с всеми дополнениями и Ikea-шкафом был выставлен на продажу на онлайн-площадке и уже через неделю нашел своего нового владельца.
Я же озадачился выбором следующего аппарата. Сайт 3dtoday.ru оказал мне в этом неоценимую помощь. После нескольких дней чтения обзоров и отзывов мой выбор пал на Flashforge Creator Pro. Заказал его напрямую от производителя со склада в Калифорнии. Если не случится никаких задержек в пути, то завтра заветная коробка будет у меня на пороге.
А пока сидел без принтера начал проектировать свой собственный CoreXY на рельсах. Вот рендер текущего состояния:

Размеры принтера будут 480 мм х 480 мм х 600 мм. Стол планирую 300 х 300. И два экструдера. Позже напишу отдельный пост об этом проекте с бОльшим количеством картинок.
Подробнее...
3Dtoday за 60 секунд от 6 июля
2017-07-06 20:07:57 (читать в оригинале)Все самое интересное на 3Dtoday за прошедший день:
Подробнее...
Подсветка стола 3D-принтера на магнитах
2017-07-06 19:29:08 (читать в оригинале)Магнитная подсветка для стола 3D-принтера.
Добрый день, коллеги!
Озадачился локальной подсветкой стола 3D-принтера. Нашел прямо чудесные фонарики с USB разъемом в FixPrice. Гибкий держатель, сам фонарик тоже с USB-папой, отстегивается от "гуся". Приделал к принтеру. Удобно, но темно.


Нашел "в запасах" две светодиодные панели - 5В, 24 светодиода, ток - 360 мА, размеры 30х80мм. Принтер лишний раз сверлить не хотелось, сделал модель для крепления подсветки на магнитах. Преимущество - съемные, можно "приклеить" на любую металлическую поверхность или просто поставить. Провода зафиксировал клипсами с теми же магнитами. В самой клипсе провод крепится резиновым кольцом. Все получилось съемное и мобильное.





Магниты использовал круглые, 10х1 мм, на фонарь - 5 шт, 1 шт. на каждую клипсу.
Покупные USB-фонарики тоже оставил, шланг гибкий, удобно при смене пластика или "прочистке" экструдера.
Питание на подсветку подал от отдельного блока питания, ибо не хотел нагружать штатный блок питания и хотелось иметь свет при выключенном блоке управления.
Блок питания нашел только на 12В, поэтому на USB подсветку понизил стабилизатором LM7805, а панели соединил последовательно и подал на них все 12В от блока питания через резистор 5 Ом. Мощность резистора должна быть не менее 5 Вт. Подключать панели к стабилизатору LM7805 не рекомендую, будет сильно греться.
Файлы stl: http://3dtoday.ru/3d-models/for-home/lighting/podsvetka_na_magnitakh/
Магниты: https://goo.gl/e1rwLa
Панели 5В: https://goo.gl/xtHtct
Панели 12В: https://goo.gl/agRyW9
Блок питания 5В: https://goo.gl/HdUQkM
Блок питания 12В: https://goo.gl/VxBfdJ
Стабилизатор LM7805: https://goo.gl/zLuQXa
В случае использования блока питания на 5В "танцы" с последовательным включением панелей и использованием стабилизатора не нужны.
Успехов!
Подробнее...
Бампер для телефона
2017-07-06 19:24:15 (читать в оригинале)
Этот проект был для меня попыткой ответить на вопрос любимого человека “ну и зачем ты купил эту фигню?”. Немного подумав, я решил, что дорогому человеку ну просто необходимо распечатать бампер для телефона. Телефон обычный PHILIPS Xenium V387. Мне хотелось во внешнем облике как-то провзаимодействовать с собственным дизайном телефона. И мне пришла в голову мысль, что если из слова “PHILIPS” выкинуть три первые буквы, то получится “LIPS”, то есть губы. И сыграть на этом. Украсить все губами.
Чтобы ничего нужного не закрыть я постарался как можно точнее отрисовать сначала модель самого телефона. В эскиз в SolidWorks скинул картинку телефона в хорошем качестве (которую нашел в интернет обзоре), обвел контуры и задал размеры – так получил точную основу. Лично об этой возможности вставлять картинки в эскиз в этой программе я узнал сравнительно недавно, и она часто бывает нужна для построения точных моделей. Кому нужно сможет вставить картинку в открытый эскиз через меню: Инструменты→Инструменты эскиза→Картинка эскиза:

Еще на поверхности готовой модели наложил те же самые картинки видов телефона и получил вот такую модельку:
Главное в ней, что видно, где какие камеры и кнопки. Ну, если совсем быть честным, то хочется иногда “наводить красоту” – подбирать текстурки, лепить надписи. При проектировании обычно это всё просто избыточная трата времени, но иногда может спасти от ошибки (от “замуровки” какого-нибудь отдельно стоящего важного элемента).
Тот ярко красный бампер, что идет в начале текста, был моим первым вариантом исполнения. Но красный цвет был забракован получателем и заменен на белый и позже бампер обрел такие очертания:
Телефон вставляется через низ корпуса и закрывается заглушкой. Для основной камеры предусмотрел шторку, чтобы избегать отпечатков пальцев:
Шторка имеет Н профиль и просто защелкивается на отверстии. Поначалу опасался, что не вставится или сломается, но в жизни как раз со шторкой проблем не возникло. Четко со щелчком ходит вправо-влево.
Для защиты экрана также заложил крышку:
Крышка должна держаться на неодимовых магнитах, которые вклеиваются в корпусе и крышке в гнезда, как показано на разрезе:
Печатал белым PLA пластиком фирмы REC, сопло 0,4 мм, температура 200 градусов, слой 0,15 (только шторка 0,1 мм).
Так как размеры поля печати у моего принтера скромные, то корпус пришлось разрезать пополам. Получилось так:
На фотографиях детали уже без поддержек и прошли первый “шкуринг” в холодной воде.
На фото ниже правый бок детали еще не обработан.
Разрез корпуса сделал слишком причудливый. Мне показалось, что если увеличить площадь разреза, то детали прочнее склеятся. Так это или нет, я не понял. Корпус склеил клеем секундой и это было ошибкой, потому что по линии склейки образовалась хоть тонкая, но заметная неровная линия, которая не убиралась даже после шпаклевания растворенным в дихлорметане PLA. После легкой шлифовки эта линия снова и снова проступала.
Теперь я знаю, что в таком случае нужно пользоваться только дихлорметаном (на момент склеивания он отсутствовал).
Пришлось воспользоваться белой аэрозольной краской, которая заодно покрыла некоторые пропуски на поверхности. Кстати в итоге нескольких итераций с покраской, я для себя определил, что главное в этом деле погуще залить проблемные места, а наплывы после просушки легко выравниваются шкуркой.
А вот с крышкой мне совсем не повезло. Под конец печати её выгнуло винтом, так как отлепился бумажный скотч, на котором она печаталась. Я хотел было её выкинуть, но не разрешило земноводное, и я попробовал её расправить. Оказалось, что PLA пластик становится пластичным под обычной струйкой горячей воды из крана. Подставляя то под горячую, то под холодную струю (для отверждения) я придал пальцами нужную форму детали.
Так что имейте ввиду, из PLA можно лепить почти как из пластилина.
Вот что в итоге получилось:



Красиво?
Если у кого то сложилось слишком благостное впечатление, то напоследок надо признаться, что с магнитами получилось не совсем гладко. Крышку они держат, но как то слабоватенько.
Вообще я пришел к выводу, что для хорошей фиксации деталей, магниты нужно закладывать в конструкции максимально близко друг к другу (идеально с касанием). А вот в верхней части крышки у меня получился некоторый сдвиг между местами посадки магнитов.
Вот некоторые говорят, что сколько водки не бери, а все равно в магазин два раза бежать. Так вот я заметил, что в 3D моделировании и печати все аналогично.
Сколько модель не крути, а чтобы нормальную вещь получить, печатать все равно нужно два раза.
Всем удачи!
Подробнее...

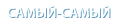

Категория «Живопись»
Взлеты Топ 5
![]() | ||
+148 |
209 |
Relazioni |
+137 |
188 |
МухО_о |
+131 |
141 |
allf |
+125 |
186 |
RouxAngel |
+123 |
142 |
kalininskiy |
Падения Топ 5
![]() | ||
-1 |
4 |
nightwishenka |
-3 |
2 |
tya-tyan_S |
-3 |
129 |
Клуб антиквариев и коллекционеров |
-6 |
3 |
antiqvar |
-8 |
170 |
Создавая пространство.. Блог декоратора Кати Саган |

Популярные за сутки
Загрузка...

BlogRider.ru не имеет отношения к публикуемым в записях блогов материалам. Все записи
взяты из открытых общедоступных источников и являются собственностью их авторов.
взяты из открытых общедоступных источников и являются собственностью их авторов.