![]() ![]() ![]()
Какой рейтинг вас больше интересует?
|
Главная /
Каталог блоговCтраница блогера 3D-принтеры сегодня!/Записи в блоге |
![]() |
|
3D-принтеры Zortrax теперь совместимы с филаментами от сторонних производителей
2017-05-30 16:54:06 (читать в оригинале)Хорошие новости для владельцев 3D-принтеров Zortrax: новая версия фирменного программного обеспечения Z-Suite позволяет создавать профили с настройками для филаментов от сторонних производителей.
Подробнее...
Слайсинг
2017-05-30 16:43:02 (читать в оригинале)Всем добрый день!
Я хотел бы поднять тему слайсинга. Кто какими слайсерами пользуется?!
Я поделюсь своими мыслями, но так же хотел бы, получить обратную связь… может кто-то интересными специфическими слайсерами пользуется.
Начну с слайсера – Cura в версии 2. Cura 1 по массовости, наверно, самый массовый слайсер. Версия 2 только набирает обороты. Чем мне он нравиться:
1. В отличии от 1 версии и от аналогов это множество настроек: можно настроить все что хочешь.
2. Возможность создать кучу профилей печати. В первой версии нужно было сохранять профили, потом открывать и т.п.
3. Удобный интерфейс и навигация.
4. Более-менее разумная расстановка поддержек.
5. Для 2-х экструдерного принтера есть возможность печати в коконе и с черновой башней.
6. Быстрый слайсинг.
Минусы
1. Нет возможности вручную расставить поддержки.
2. Сложность добавления 2-х экструдерных принтеров (можно сделать через копирование/редактирование профилей, предустановленных 3d принтеров).
3. Нет возможности подключиться к принтеру, кроме Ultimaiker.
4. Неудобный просмотр нарезанной модели.

Второй слайсер, которым я пользуюсь – это Simplify3D. Это наиболее используемый мной слайсер, поскольку все преимущества, что я описал выше для Cura и для Simplify3D присущи, к тому же у него нет выше описанных недостатков. Отличительной особенностью этого слайсера является грамотная расстановка поддержек, можно так же самому расставить поддержки. Кроме того, очень удобен просмотр нарезанной модели, даже есть возможность симуляции печати.
Самый главный недостаток Simplify3D – это платная лицензия. Но в инете есть много ломаных версий.

Далее следовало написать про Repetier-Host, slic3r, Kissliser и т.п. Но я ими не пользуюсь, поскольку для меня они неудобны в использовании. Из них можно выделить программку Repetier-Host, которая позволяет производить настройку 3d принтеров.
Теперь об «экзотике»…
Я очень часто пользуюсь програмкой ideaMaker производителя принтеров raise3d (https://www.raise3d.eu). Она бесплатна. ideaMaker по функционалу очень похожа на Simplify3D, но по интерфейсу, мне кажется, намного удобнее! В ней так же можно расставлять самому поддержки. Недавно добавили поддержку русского языка.

Недостатки, которые я обнаружил, в основном касаются 2-х экструдерной печати:
1. Нет возможности печати с черновым столбиком – только с коконом или без.
2. При печати в коконе, при смене сопел, почему-то печать начинается с детали, а не с кокона, в результате из-за ретракта возникают сопли на детали.
Ну и общий недостаток – производитель raise3d указывает на то, что в ideaMaker можно исправлять STL файлы (дыры и т.п.), но по факту можно исправить STL только нарезанные в самой ideaMaker.
Но тем не менее программка очень хорошая, я ей пользуюсь чаще чем Cura.
И еще одна «экзотика»…
Когда я печатал на одном экструдере на принтере HORI GOLD я всегда сталкивался с не очень хорошим качеством печати при поддержках. Я перепробовал много слайсеров… но ничего стоящего не нашел. Потом наткнулся на прогу Meshmixer с древовидными поддержками, результат стал лучше... И сосем недавно обнаружил, что производитель HORI выпустил свой слайсер (http://www.hori3d.com:81/software.html). Отличительная особенность этого слайсера - это автоматичное формирование древовидных поддержек (помимо обычных). А также формирование автоматически и вручную точечных поддержек. Сам слайсер простенький с предустановленными настройками для принтеров HORI, но можно настроить и любой другой. Так же заметил такую особенность что этот слайсер наиболее точно прогнозирует время печати. Все остальные, которыми я пользуюсь врут +/- час, а то и два.

Мое мнение - слайсер HORI если и не лучший, то один из лучших для одноэкструдерников.
У меня все, поделитесь своим опытом слайсинга…
Подробнее...
Дистанционная разработка держателя планшета.
2017-05-30 14:23:24 (читать в оригинале)Напечатав кучу тестовых кубиков и полезных безделушек для дома я задумался как применить 3D принтер по работе. Коллега как-то высказывал мысли по поводу желания иметь фирменный брелок. Откопав в избранном статьи о двухцветной печати я сделал модельку в фирменных цветах и распечатал ее.
Безделица была передана хозяину, который был очень рад

Но хотелось чего-то большего. И тут я вспомнил как год назад мы мучились на складе прикрепляя планшеты на мачту ричтрака. Готовых держателей нет, поэтому пришлось брать автомобильные и с помощью стяжек и прочих приспособлений как-то фиксировать. Выглядело это не очень надежно, но работало. Еще одна сложность - внешнюю батарейку пришлось расположить в одном из отделений ричтрака, а к планшету тянуть провод питания, который иногда задевали и он со свистом вылетал из планшета.
Вот где можно использовать 3D принтер по прямому назначению - создать уникальный держатель, который решал бы поставленные задачи. Была только одна проблема - планшеты и техника в Саратове, а я в Москве

Предложил идею работником склада и после волшебного слова "бесплатно" они с радостью согласились снять все нужные размеры


Получив размеры планшета Samsung Galaxy Tab S2, батарейки и стойки ричтрака я приступил к моделированию держателя в Solidworks. Не зная насколько все точно замерено надо было с одной стороны сделать запасы под возможные допуски, с другой стороны планшет должен был крепиться довольно крепко.
В итоге был создан первый макет. Для его демонстрации я создал небольшое видео и выслал заказчику.
Загрузка плеера
Проект был одобрен и настала очередь печати. Тут я понял преимущество стола 300х200, на который детали держателя влезали целиком без необходимости разрезать на части.
Для тестового экземпляра был выбран недорогой черный пластик FDplast, который показал себя вполне неплохо.
Самым долгим была печать основания - печать заняла 10 часов. Были опасения, что без корпуса ABS захочет расслоиться или отлипнуть, но к счастью все прошло успешно.
Все запчасти были распечатаны, но проверить на деле не было возможности. С удивлением обнаружил, что вместо Samsung в держатель отлично влезает iPad mini

Ребята со склада одобрили результат по фотографии и держатель был передан человеку, который из Москвы выезжал в Саратов. По закону Мерфи человек держатель забыл взять с собой и процедура немного растянулась.
Когда изделие наконец-то добралось до пункта назначения мне начали скидывать фотографии испытаний. Сам планшет подошел отлично, но вот кнопки питания и регулировки громкости нажимать было не удобно. Я даже и не думал, что их надо нажимать и сделал прорези чтобы их не придавило, но оказалось что кнопка питания нужна. На складе долго не думали и отпилили ненужные части



Модель была сразу немного переделана.
Далее пошли примерки уже на технике.


Все встало как и планировалось. Лишь в одном месте попросили на пару миллиметров увеличить расстояние.
Далее уложили внешнюю батарею и получилось все как и задумывалось - все в одном месте без лишний кабелей.

На вопрос "Ну как?" в Skype получил ответ:

Этим проектом заинтересовался генеральный директор компании и появилась мысль начать торговать 3D принтерами. Тут я сразу предупредил, что это пока не бытовой прибор и надо сразу готовить грамотных консультантов и мастеров по ремонту техники для возможности быстрого исправления мелких недочетов. Также накидал ссылок на достойные варианты для продвижения.
Возможно с моей подачи в славном городе Саратове начнут продажи 3D принтеров в розничной сети, но пока это только планы и чем все закончится я сообщу чуть позже

Подробнее...
Конференция по 3D-печати в Сколково
2017-05-30 13:41:43 (читать в оригинале)[LEFT]В Сколково стартует международная конференция, посвященная трехмерной печати композитов. Основным ее организатором и идейным вдохновителем выступает сколковский стартап «Анизопринт», резидент кластера передовых производственных технологий, ядерных и космических технологий Фонда «Сколково». «Анизопринт» разработал и продвигает технологию трехмерной печати деталей из пластика, армированного непрерывными волокнами. Этот метод позволяет изготавливать образцы композитного материала, по прочности и жесткости превосходящие мировые аналоги.
Подробнее...
ABS под обстрелом
2017-05-29 17:51:11 (читать в оригинале)Наступившее тепло и пяток достаточно свежих ABS-пробников сподвигли на повторение идеи отправится на полигон. Пострелять.
Пять образцов, пять производителей. Готовим к печати пять тестовых пластин. За одно получим краткий обзор материалов.
Дабы по максимуму создать одинаковые исходные условия, печать производилась в один день. А то бывает, то один образец отпечатаешь, отложишь. Потом второй нарисуется, там то, другое. На этот раз все в русле равенства и братства ABS.

Печать производилась на принтере Hephestos, дооборудованным нагревательной платформой. Стекло 2 мм, чистое. Температура в помещении ниже 19 градусов. Так получилось. Но тем более было интересно понаблюдать как поведут себя материалы в подобных условиях.
Для отстрела печаталась тестовая пластина 70х70 мм, толщиной 3мм. Толщина стенок, верха-низа - 1,2 мм. Заполнение 45%. Скрорсть первого слоя 20, последующих 70 мм/сек. Толщина слоев - 0,25мм
1. НИТ- Волгоград
Я специально выделил город, так как производство переместилось из столицы чернозема на берега Волги. По крайней мере послыка с тестовыми образцами пришла именно оттуда и по качеству печати филамент совершенно отличается от воронежского материала. От слова совсем.
Температура экструдера 255 градусов, можно и к 245 уйти. Но я тут перестраховался, о чем немного позже пожалел. Температура стола - 97градусов.
Запах ABS отсутствует вообще. Что так, в мотке, что при печати. Можно нос и под сопло сунуть. Нет запаха. Адгези к столу отличная. Первый слой лег плотно. Межслойная так же на высоте. Спекаемость слоев на достойном уровне. Материал обладает хорошей текучестью. Во время печати отсутствует характерное потрескование пластика означающее, что деламинация на подходе, ожидайте. Но при завышенной температуре, как в моем случае, после печати и снятии со стола края начали потихоньку уходить вверх, хотя первый слой остался в горизонтали. Готовая модель отстает легко, всей площадью одновременно. Снимать следует при пороге ниже 50 градусов, так как материал все еще пластичный. При обработке абразивами ведет себя как PLA, но "полосатость" убирается достаточно хорошо. Последующая обработка наждачной бумагой трудностей не представляет. При обработке запах ABS чувствуется, но не навязчиво.
К интересным особенностям стоит отнести, что верхний, заключительный слой, при грамотно подобранном перекрытии слоев практически не требует постобработки. Фактически отсутствует "ребристость" и по тактильным ощущуения поверхность гладкая, глянцевая. Если нет желания возится со "шкурингом" - приемлимый вариант.

2. НС-19 "Спутник"
На прошедшей в прошлом году выставке Принт-Экспо я был впечатлен размерами деталей представленными на стенде производителя. Точнее нет, не размерами, а областью применения. Литейка! В опоку под прессом! Напросился на образцы. Поделились.
Температура экструдера 240 градусов, дал по максимуму. Запах при печати отсутствует. Стол. Хм-м, стол.
"Братья и сестры по экструдеру. Герои битв с деламинацией и победители адгезии! Воистину написанные 90 градусов для стола - Истина". Если серьезно то так и есть. Печатал на столе в 90. Потом замучился ждать отлипания, можно было и на 80 ставить. Отдирал уже ниже 50, но пластик к этому моменту "заматерел". Снимался всей площадью. Так что, как вы понимаете, адгезия к стеклу серьезная. Да и вообще, сама печатать со стороны выглядит впечатляющее. Сопло наносит материал этакими бугристыми мазками. Броню видели? Вот считайте, что нечто подобное получается и при печати.
Межслойная адгезия на высоте. Спекаемость слоев хорошая. Результат выглядит добротно. Обрабатываемость абразивными материалами затруднений не вызывает.

3. "GEO" Print-Product.
На той же выставке стал обладателем тестовых образцов новой линейки от питерской компании.
О производителе рассказывать, я думаю, не стоит. Известен. В порочащих филамент связях не замечен.
Температура эктрудера - 245 градусов. Стол - 98. Как обычно, без писку и шуму пошла печать. Легкий запах в районе экструдера витал.
В общем рутина. Материал лег на стекло и пошел периметр наматывать. Но уж больно приставка GEO меня свербила. Мда-а, кажись сглазили. При традиционно хорошем качестве печати, тем не менее, материал излишне чувствителен к внешней температуре и нагретой платформе. 100 градусов для стола - это тот минимум, когда можно работать с деталями больших размеров. Если открытая платформа, то окружающий воздух должен уходить за двадцатку. При моих параметрах печати деламинация пошла уже после высоты 2мм. Сначала не очень заметно (потрескивание выдало), но затем все явственнее и явственнее. В защиту материала хочу сказать, что традиционно для Print-Product оный держался до конца и не сорвался. Цыпучий. Но до М6 ему все таки пилить и пилить (пусть переплюнет +16 воздуха при 98 платформы).
Тем не менее, при всех своих язвительных замечаниях, должен отметить, что само качество отпечатаной детали хорошее. Спекание слоев качественное. Печать ровная. Отлично поддается обработке абарзивами. Можно сказать легко.
Возможно колдуны от лака и клеев добьются полного прилипания, но, как мне думается, сей материал явно для закрытых платформ предназначен.

4. ABS REC
И этот производитель хорошо известен широкому кругу печатающих. В мои цепкие лапки он все ни как не попадался, но последняя выставка принесла удачу. Образцами разжился.
Температура экструдера - 233 градуса. Стола - 98. Запах в районе печати присутствует.
Таки знаете, на чистый стол этот пластик прилип и даже дал себя размазать по все поверхности. Хороший пластик. Но как и в случае с GEO любовь закончилась гораздо раньше чем экструдер уполз на свое место. Характерное потрескование стало сигналом к первым порывам деламинации. На полутра миллиметрах процесс стал явсвенным и в последующем скачущий по загибающимся в верх краям экструдер вызывал дрожь. Но, тем не менее, модель держалась и отставать от стекла категорически отказывалась. Так и просидели до конца печати играя в гляделки. Пластик почти удержался, так как в момент последнего движения экструдера к парковке сдвиг никакой роли уже не играл.
Нормальный пластик, но, как и в предыдущем случае, требует соответствующих условий для длительной печати. Возможно, что я мог и со скоростью переборщить, при таких условиях печати. Спекаемость слоев хорошая, но чуть началасть деламинация с гулянием высот, все. Можно как по годовым кольцам дерева отследить все нюансы как печати, так и оборудования. Строгий пластик. Хорошо поддается обработке образивами, но, как и в случае с печатью характерный запах ABS дает о себе знать. Вполне себе "рабочая лошадка".

5. ABS Prostoplast
Температура экструдера - 245. Стол - 98. Запах при печати был как напоминание. Тонкий, едва уловимый, у сопла, но сразу ясно - ABS.
И этот материал спокойно примостился на чистом стекле дав себя уговорить не выпендриваться, хотя бы на начальном этапе.
Слои ложились ровно и аккуратно. Межслойная адгезия хорошая. Текуч.
Вполне себе выдержал печать до 2мм, затем стал из под тишка один край загибать. Получилась какая то "однобокая" деламинация. Но, до окончания печати модель вытерпела. Так же как и у REC гуляние высоты определяется сразу. Переходный слой волнистый. Потом все становится ровным. Материал теплоемкий. При снятии с платформы (точнее, он сам отскочил на 95) уже обладая твердостью, тем не менее очень горячий. Остывает медленно. Хорошо поддается абразивным материалам.

Сразу скажу, что экспресс-отчет не претендует на истину в последней инстанции. Все вышеописанные материалы, лично мне, понравились не смотря на определенные огрехи. Печать шла "в лет", без предварительного "обнюхивания" и подбора оптимальных значений. За исключением температуры экструдера для каждого пластика. Но без этого, как вы понимаете, нельзя обойтись.
С пластинами для стрельбы закончили, теперь перейдем непосредственно к самому процессу.
В качестве оружия выступает пневматическая винтовка МР-512. Ни каких шаманств над ней не проводилось. Пули GAMO двух видов. Остроконечная и тупоголовая.
В течении прошлого года ставился ряд эксперементов по определению пробития разных видов пластика (самый первый пробный шар здесь). Как оказалось, ABS достаточно стоек к подобного рода "издевательствам". Практически до "в упор". По этому в этот раз решено было произвести каскадное испытание. Первоначально стрельба будет вестись с дистанции 15 метров, затем десяти. Дальше, если участник будет в состоянии продолжить, дистанция сокращается до пяти метров. Потом посмотрим. Хотя, был у меня один "индивидум", который выдержал выстрел с расстояния метр, но на восмидесяти сантиметрах пробился.
Все. Зачехляемся. Поехали на полигон.
Продолжение следует.
Подробнее...

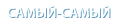

Категория «Священники»
Взлеты Топ 5
![]() | ||
+4 |
68 |
Позже,чем кажется |
+1 |
2 |
священник Стефан Красовицкий |
|
|
|
|
|
|
|
|
|
Падения Топ 5

Популярные за сутки
Загрузка...

BlogRider.ru не имеет отношения к публикуемым в записях блогов материалам. Все записи
взяты из открытых общедоступных источников и являются собственностью их авторов.
взяты из открытых общедоступных источников и являются собственностью их авторов.