В этой публикации рассказывается о технологии порошкового покрытия разработанной компанией Jotun. Основой технологии является эпоксидное порошковое лакокрасочное покрытие с высоким содержанием цинка Corro-Zinc 97, разработанного в качестве грунтовочного покрытия на фасфатированные или обработанные пескоструйным методом стальные поверхности. Corro-Zinc 97 даёт превосходную стойкость к коррозии, превосходные механические свойства и межслойную адгезию, очень хорошие дегазирующие свойства, очень хорошую контурную кроющую способность и хорошую растекаемость.
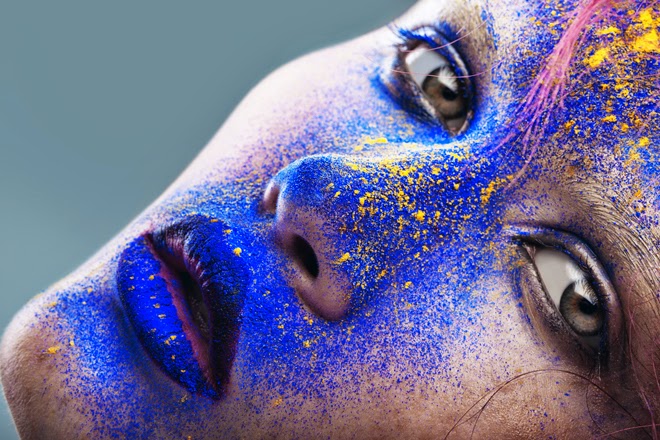 |
На фото утомившийся лаборант после тяжёлого трудового дня проведённого в поисках наилучшей технологии защиты металлических поверхностейпорошковыми покрытиями. |
Для защиты стальных поверхностей в условиях эксплуатации с наличием агрессивной среды которой может являться морская вода, химические реагенты для борьбы с обледенением автодорог, сельскохозяйственные удобрения, активные моющие вещества или в том случае если необходимо защитить несущие стальные конструкции зданий и сооружений с повышенными требованиями к надёжности, обычно применяются металлические защитные покрытия, получаемые различными способами. Наиболее распространённым методом защиты стальных конструкций с повышенными требованиями к антикоррозийной защите является горячие оцинкование и набирающее популярность диффузионное оцинкование. Эти способы имеют технологические ограничения и высокую стоимость, обусловленную крупными капиталовложениями в оборудование и большими эксплуатационными расходами из-за высокой энергоёмкости процессов.
Технологический процесс производства защитно-декоративного порошкового покрытия с использованием цинкосодержащего грунтовочного слоя:
- Подготовка поверхности
Общее качество лакокрасочного покрытия зависит в значительной степени от качества предварительной подготовки поверхности.
Способы предварительной подготовки поверхности в зависимости от предъявляемых требований к коррозийной стойкости:
Средняя стойкость (категория коррозии C3*)
Фосфат железа или пескоструйная очистка (SA 2.5 с профилем 40-80 мкм).
Этот способ подготовки поверхности рекомендуется применять для металлических изделий работающих внутри помещений.
Высокая стойкость (категория коррозии C4*)
Фосфат цинка или пескоструйная очистка (SA 2.5 с профилем 40-80 мкм) в комбинации с фосфатом железа.
Этот способ подготовки поверхности рекомендуется применять для металлических изделий работающих в сельской местности вдали от автомобильных дорог, не контактирующих с морской водой.
Очень высокая стойкость (категория коррозии C5 - M/I*)
Пескоструйная очистка (SA 2.5 с профилем 40-80 мкм) в комбинации с фосфатом цинка, в качестве альтернативы возможна замена цинкафосфатирования конверсионными покрытиями Oxsilan или BONDERITE M-NT.
Этот способ подготовки поверхности рекомендуется применять для металлических изделий работающих в контакте с морской водой, судовых конструкциях, конструкциях работающих в непосредственной близости от автомобильных дорог, а также для защиты деталей транспортного машиностроения.
* Обращаться к стандарту ISO 12944-2 (classification of environments - классификация среды)
2. Сушка изделия
После нанесения конверсионного слоя изделие промывается деми водой, остатки которой необходимо удалить с поверхности. Сушка изделия может производится тремя способами:
- Циркулирующем горячем воздухом в сушильной камере 20-30 мин. при температуре 120-140ºС. При использовании этого метода сушки необходимо обеспечить охлаждение изделия перед нанесением порошковой краски до max. 40ºС. Именно охлаждение изделия, а не поверхности изделия, так как если толщина металла значительная, то при охлаждении струями воздуха, поверхность металла охлаждается, а внутри он остаётся горячем. Если температура поверхности металла при нанесении будет более 40ºС, будет происходить процесс неравномерной преждевременной полимеризации и в лучшем случае вы получите неравномерную шагрень.
- Струями горячего воздуха. Этот метод менее эффективен, более энергоёмкий, менее производительный. Но позволяет избежать перегрева поверхности изделия и практически сразу отправлять изделие в камеру нанесения порошковой краски.
- Сушка изделия на спокойном воздухе. Это самый дешевый способ, требует наличия чистой зоны сушки с минимальной влажностью воздуха. При поточном производстве этот способ является нерациональным.
3. Нанесение первого (грунтовочного) слоя Corro-Zinc 97
Технология нанесение Corro-Zinc 97 не чем не отличается от технологии нанесения обычных порошковых красок. Corro-Zinc 97 изготавливается для электростатического или трибостатического распыляющего оборудования. Температура поверхности окрашиваемого металла - max. 40ºС.
4. Полимеризация Corro-Zinc 97
Режимы полимеризации:
10 минут при температуре объекта 180ºС
6 минут при температуре объекта 200ºС
Рекомендуется провести частичное отверждение
Corro-Zinc 97 перед тем, как наносить верхний слой лакокрасочного покрытия (3-5 минут при температуре объекта 180ºС или 2-3 минуты при температуре объекта 200ºС). Затем композиция полимеризуется в соответствии со спецификацией верхнего слоя лакокрасочного покрытия. Испытания показали, что при частичной предварительной и полной последующей полимеризации совместно с верхним слоем,
Corro-Zinc 97 + финиш Corro-Coat PE/PE-F даёт превосходные результаты.Свойства межслойной адгезии и полная композиция полимеризации всегда должы быть проверены. Нанесение верхнего слоя лакокрасочного покрытия должно производится не позднее, чем через 12 часов после нанесения Corro-Zinc 97. Рекомендуется использовать наиболее короткий интервал.
5. Охлаждение изделия
После частичной полимеризации грунтовочного слоя Corro-Zinc 97, изделие необходимо охладить до max. 40ºС на спокойном воздухе либо методом обдува. При планирование производства следует учитывать факт того, что чем ниже интервал времени между нанесением слоёв, тем выше качество покрытия. Максимальный интервал - 12 часов.
Учитывая факт того, что переход с одной краски на другую, является времяёмким, при нанесении порошка Corro-Zinc 97 и Corro-Coat PE в одной камере, для повышения производительности следует планировать производство таким образом, чтобы количество "подвесов" деталей соответствовало производительности операционного узла в интервале 12 часов.
6. Нанесение верхнего слоя Corro-Coat PE
Технология нанесение Corro-Coat PE не чем не отличается от стандартных методов нанесения порошковых красок. Corro-Coat PE изготавливается для электростатического или трибостатического распыляющего оборудования. Температура поверхности окрашиваемого изделия - max. 40ºС.
7. Полимеризация Corro-Coat PE
Режимы полимеризации:
20 минут при температуре объекта 170ºС
12 минут при температуре объекта 180ºС 8 минут при температуре объекта 200ºС
При полимеризацие Corro-Coat PE грунтовочный слой Corro-Zinc 97 полимерезуется полностью.
Метод частичной полимеризации грунтовочного слоя позволяет снизить энергозатраты и повысить производительность полимеризационной печи.
Технические характеристики Corro-Zinc 97
Ниже приводятся технические характеристики, типичные для Corro-Zinc 97, нанесённые на стальные листы толщиной 0,8 мм, с предварительно нанесённым цинкофосфатным покрытием 60 - 80 мкм.- Адгезия по EN ISO 2409 (ГОСТ Р 54563—2011) (2 mm) - Метод перекрёстных надрезов Gt0 (100% адгезия).
- Прочность при ударе ASTM D 2794 (5/8" шар) - ˃ 60 дюйм - фунтов без нарушения лакокрасочного покрытия.
- Изгиб по Эриксену (мм) по EN ISO 1520 - Удовлетворительно, 5 мм без нарушения лакокрасочного покрытия.
Технические характеристики Corro-Coat PE
Ниже приводятся технические характеристики порошкового покрытия Corro-Coat PE серии 50 толщиной покрытия 65 микронов, нанесённого на стальной лист холодного проката толщиной 0,8 мм, с предварительно нанесённым цинкофосфатным покрытием 60 - 80 мкм.
- Адгезия по EN ISO 2409 (ГОСТ Р 54563—2011) (2 mm) - Метод перекрёстных надрезов Gt0 (100% адгезия).
- Прочность при ударе ASTM D 2794 (5/8" шар) - ˃ 60 дюйм - фунтов без нарушения лакокрасочного покрытия.
- Изгиб по Эриксену (мм) по EN ISO 1520 - Удовлетворительно, 5 мм без нарушения лакокрасочного покрытия.
- Гибкость EN ISO 1519 - Большинство изделий могут выдерживать изгиб до диаметра 12 мм - без нарушения лакокрасочного покрытия
- Твёрдость плёнки EN ISO 2815 - Твёрдость измерена вдавливанием по методу Бухгольца - более 70.
- Антикоррозийная защита (соляной туман) ASTM B 117 -Превосходно. Измерено путём наблюдений за образованием пузырьков и потери адгезии.
- Устойчивость к влажной атмосфере DIN 50017 - Превосходно. Измерено путём наблюдений за образованием пузырьков и потери адгезии.
- Устойчивость к УФ излучению ASTM G 154 (UVB-313) - Превосходно. Измерено путём наблюдений за сохранением цвета и блеска.
Публикация в работе, скоро будет продолжение